中空ドリルの導入と応用展望
中空ドリルビット (マルチエッジ鋼板ドリル、コアドリルとも呼ばれる) は、マルチエッジの円形切削に効率的なドリルビットです。穴あけ径は12mmから150mmまで対応します。これらは主に、鉄骨構造工学や鉄道輸送などの鉄骨コンポーネントの穴あけに使用されます。、橋、船舶、機械製造、航空宇宙およびその他の穴加工分野で、その穴あけ性能は従来よりも大幅に優れています。高い穴あけ効率、軽くて省力な穴あけが特徴の両刃ツイストドリル、多刃鋼板ドリル、マグネットシートドリルなどの大型ワークの多方向穴あけが可能なマッチングツールです。操作は便利で柔軟であり、施工時間を効果的に短縮し、現代の鋼部品の穴あけや環状溝加工に最適なツールとなっています。
1.カットへの影響Edit Broアドキャスト?
中空ドリルビットは、より携帯工具に適した穴加工工具です。ただし、中空ドリルは製造工程が比較的複雑で止まり穴の加工ができないため、金属の切削加工にはあまり使用されていません。これらは通常、大径または貴金属ワークの貫通穴を加工する場合、または穴あけ装置の出力が制限されている場合にのみ使用されます。。そこから中空ドリルには標準品が存在せず、特殊材料の加工に使用される中空ドリルはほとんどが自社開発となります。
バックアングルef影響する
2.レーキの効果切削力にかかる角度は?
すくい角の変化により切りくず材の変形度合いが変化し、切削抵抗が変化します。g切りくずの変形が大きいほど、切削抵抗は大きくなります。切りくず変形が小さいほど切削抵抗は小さくなります。すくい角が0°~15°の範囲で変化すると、切削抵抗補正係数は1.18~1の範囲で変化します。
3.すくい角の影響ドリルの耐久性については?
ドリルのすくい角を大きくすると、工具先端の強度や放熱量が低下し、工具先端にかかる応力にも影響します。すくい角が正の値の場合、工具先端は t の影響を受けます。o 引張応力;すくい角が負の値の場合、工具先端には圧縮応力がかかります。すくい角の選択が大きすぎると、ドリルの切れ味は向上し、切削抵抗は低減できますが、工具先端にかかる引張応力が大きくなり、工具先端の強度が低下し、簡単に壊れてしまいます。切削テストでは、過度のすくい角により多くのドリルビットが損傷しました。しかし、可搬型ボール盤は被加工材の硬度や強度が高く、主軸や機械全体の剛性が低いため、すくい角が小さすぎると穴あけ時の切削抵抗が増加してしまいます。主軸が振動し、加工面に明らかな振動が現れます。ラインが傷つくとドリルビットの耐久性も低下します。
5.カットペロマンへの影響ce
逃げ角を大きくすると逃げ面と切削材料との摩擦が減少し、加工面の押し出し変形を軽減できます。ただし、逃げ角が大きすぎると、bl強度や放熱能力が低下します。
逃げ角の大きさはドリルビットの耐久性に直接影響します。穴あけプロセス中のドリルビットの主な摩耗形態は、機械的傷と相変化摩耗です。機械的磨耗を考慮すると、切削寿命が一定の場合、逃げ角が大きいほど、切削時間は長くなります。相変化摩耗を考慮すると、逃げ角が大きくなると放熱能力が低下します。ドリルビットの性質。ドリルビットが摩耗すると、逃げ面の摩耗領域が徐々に広がり、切削力が徐々に増加するため、摩擦熱が徐々に増加し、ドリルビットの温度が上昇します。温度がドリルビットの相転移温度まで上昇すると、ドリルビットが急速に摩耗するようになります。
6.研ぎの効果プロセス
中空ドリルビットは使用量が少なく、加工バッチも小さくなります。したがって、ドリルビットを設計する際には加工技術の問題を考慮し、可能な限り共通の加工設備および共通の工具を使用して加工および刃付けを行う必要があります。チップフローがパフォーマンスを向上させます。流出過程において、切りくずはすくい面で絞られ、こすられるため、さらに変形。切りくず底部の金属が最も大きく変形し、すくい面に沿って滑り、切りくず最下層が長くなり、様々なカール形状が形成されます。中空ドリルビットを使用して穴を開ける場合、切りくずの除去を容易にするために、切りくずをチップまたはストリップに切断する必要があります。加工や研ぎを容易にするために、すくい面はチップブレーカのない平面として設計する必要があります。使用中にすくい面を再研磨する必要はありません。中空ドリルビットの逃げ面は再研磨が最も容易であり、摩耗速度が最も速い面でもあります。したがって、中空ドリルの刃の研ぎは逃げ面を研ぐことによって行われます。二次逃げ面は、内部二次逃げ面と外部二次逃げ面とに分割される。再研磨の観点から見ると、内外補助逃げ面の再研磨は容易ではないため、補助逃げ面は再研磨しないように設計する必要がある。
7.切削液とドリルビット
中空ドリルビットの最大の特徴は、加工中に穴の内部コアが切断されないことです。そのため、中空ドリルの切削量はツイストドリルに比べて大幅に少なく、必要な穴あけ動力や切削時の発熱も少なくなります。ハイス鋼中空ドリルビットで穴あけ加工を行う場合、加工領域の温度がドリルビットの硬さに大きな影響を与えるため、穴あけ加工中に冷却剤を使用して冷却する必要があります(冷却剤を使用しない場合、ドリルはビット摩耗は主に相変化摩耗であり、最初は急速に摩耗します)。まずは私たち外部スプレー冷却による。しかし、ドリルビットステーションは横軸方向に加工されているため、ドリル刃の刃先にクーラントが入りにくくなっています。クーラントの消費量が多く、冷却効果が十分ではありません。ドリルリグのスピンドル構造が再設計され、外部スプレー冷却から内部スプレー冷却に変更されました。中空ドリルの芯からクーラントを注入するため、クーラントがスムーズにドリルの刃部に到達し、クーラントの消費量を大幅に削減し、冷却効果を高めます。
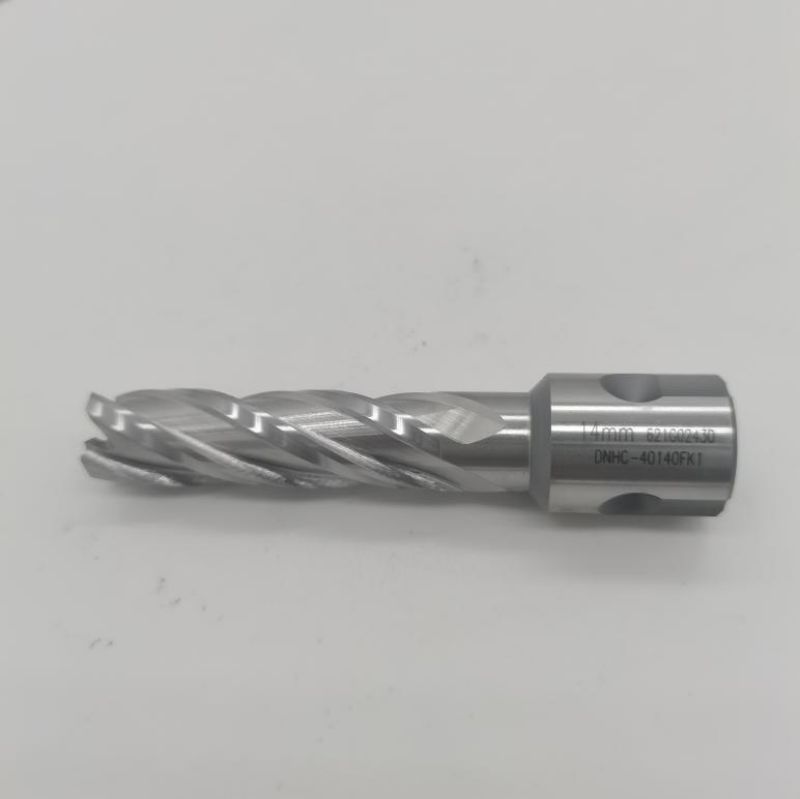
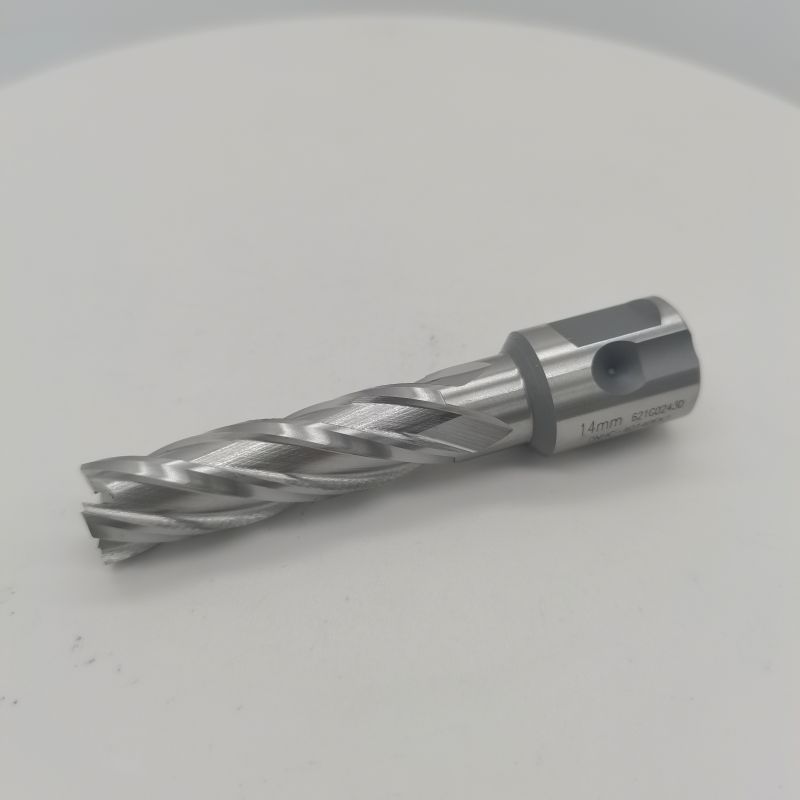
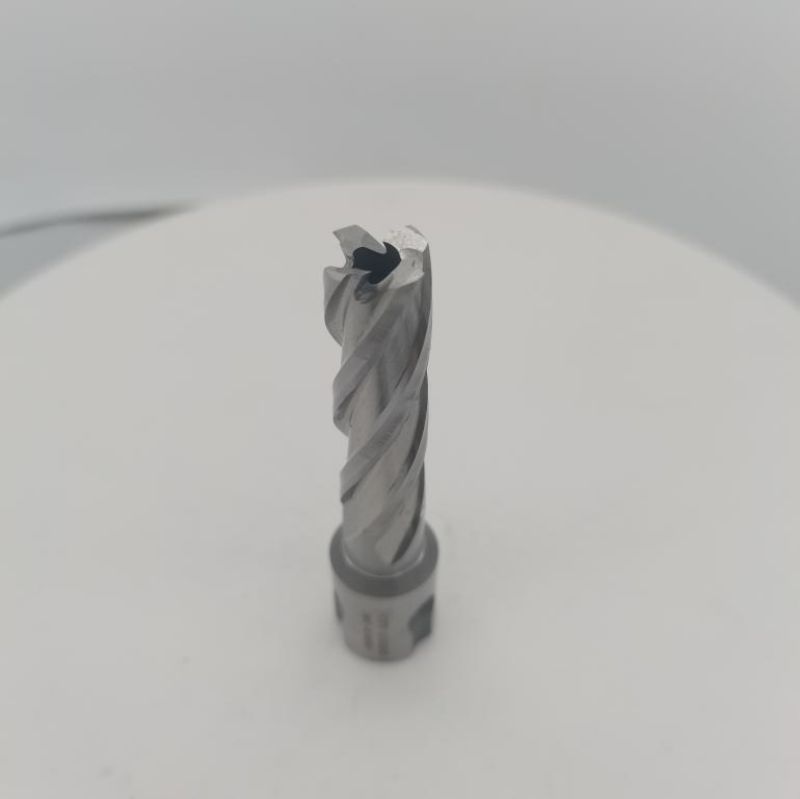